
Thread the string through the holes in the plastic spring. Then slide the 1½-inch PVC scrap over the pipe and cable ties. Slide the plastic spring onto the pipe, over the cable ties, and up against the pipe clamp. Remove the bottle from the end of the pipe.Thread the end of a 4-foot piece of string through the hole and tie a knot on it to keep it from coming out. Drill a small hole in the side of a short scrap of 1½-inch PVC pipe.This spring will hold the trigger in position until you’re ready to launch. Flatten the bottle section without creasing it and cut a 1¼-inch hole through both sides.
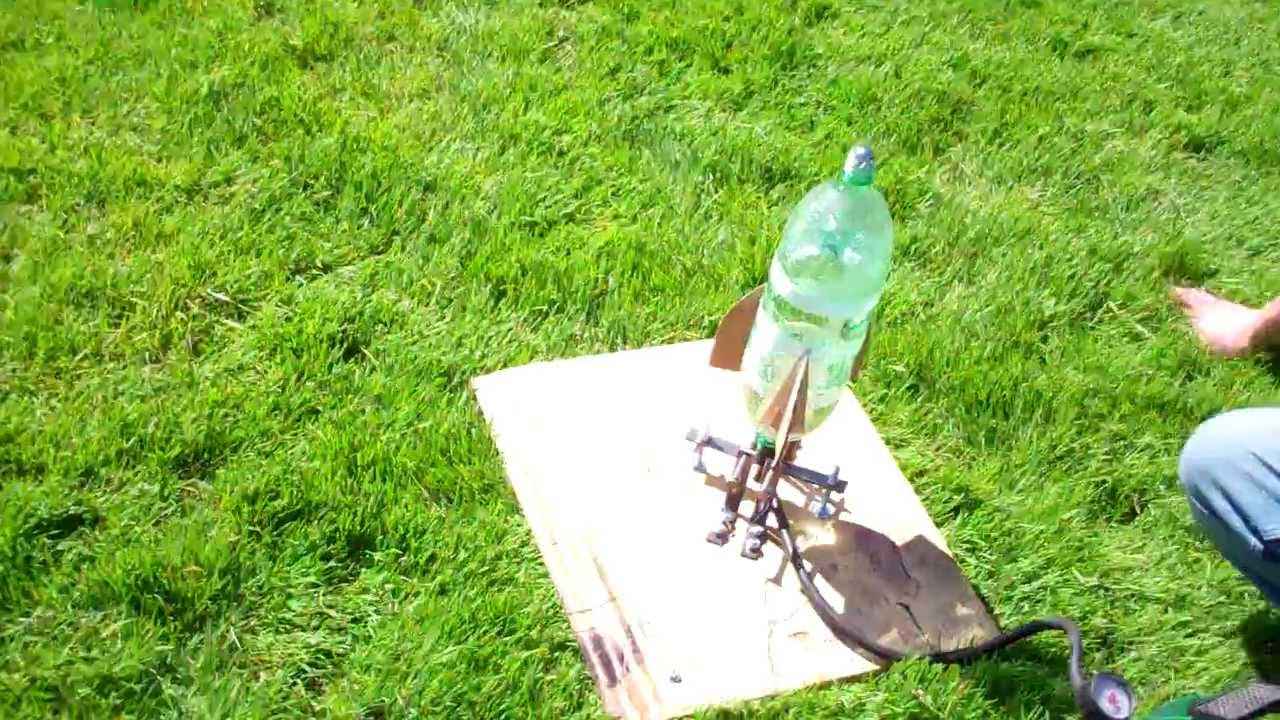
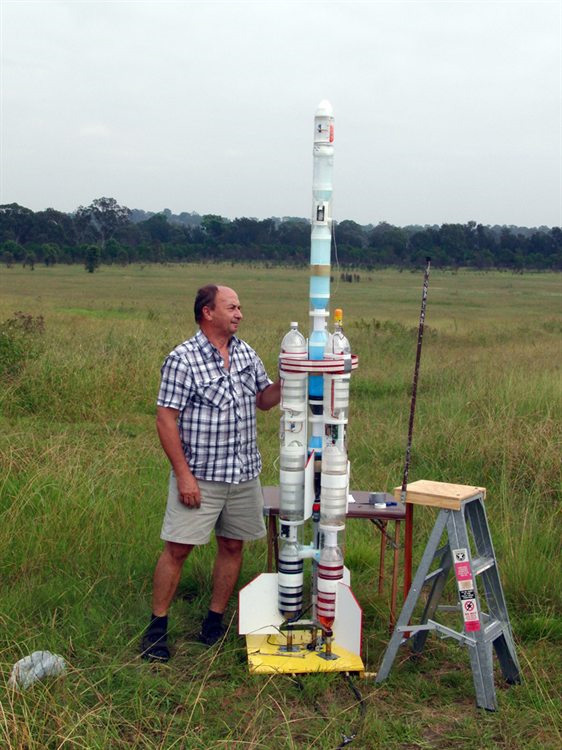
Some design changes, like shorter suspension lines, lightweight material, and neat folding techniques, can help speed up the deployment of your parachute. This takes time, so if your rocket does not reach enough altitude, your parachute might not have enough time to open up and do its job. For a bottle rocket, air resistance has to knock off the nose cone, causing the suspension lines to unravel and the parachute to unfold. Parachutes are used to slow down the fall of a rocket to reduce the risk of damaging the rocket as it touches the ground.

More mass leads to a larger force pulling the rocket down, resulting in a lower apogee. A more aerodynamic shape reduces drag, which means less force slowing the rocket down, which results in a higher apogee. Creating more pressure in the bottle before launch will increase the thrust, and thus lead to a higher apogee. The highest point of the flight path is often called the apogee. In rocketry, the force that pushes the rocket forward is called thrust, and the air resistance is called drag. Scientists use several units to quantify pressure, but it is mostly commonly expressed in pounds per square inch (psi) on your bicycle pump. Just like with the fire hose, the more pressure that is put on the water, the faster the water comes out and the bigger the push on your bottle rocket. You should have been able to deploy a parachute, even when packed in a nose cone, when using 40 psi pressure at launch. If you pack the parachute in a nose cone, make it lightweight so it blows off easily. To keep the deployment time short, pack the parachute neatly and keep the suspension lines short. This all needs to happen before the parachute touches the ground. The additional mass, and the change in the rocket's aerodynamics will slightly change the maximum altitude the rocket can reach.Ī bottle rocket does not have a parachute ejection system like real rockets, so the air has to push off the nose cone if there is one, allowing the suspension lines to unwind and the parachute to unfold. If the nose cone was heavy compared to the mass of the rocket, you might have observed a decrease in altitude.Īdding a parachute adds some mass, but it considerably increases the chance to recover the rocket undamaged. Unfortunately, a nose cone adds some mass to be pushed up. A rocket with a nose cone has an easier time pushing the air aside and making itself a path through the air, and thus, it usually reaches a higher altitude. When you cranked up the pressure inside the bottle from 20 psi to 40 psi, your rocket probably reached a higher altitude.īy adding fins-even small fins-you probably noticed the rocket took a straighter path to its highest point (the apogee), and no longer tumbled down, but flew straight down.īy adding a pointy, sleek nose cone, you made the rocket more aerodynamic.
